Comprehensive Guide to Dock Repair Costs
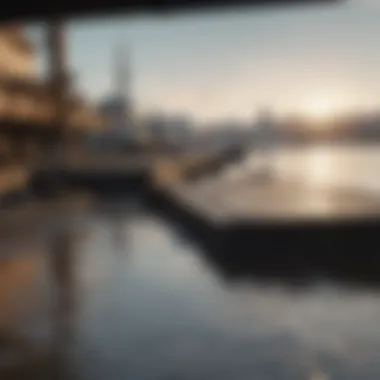
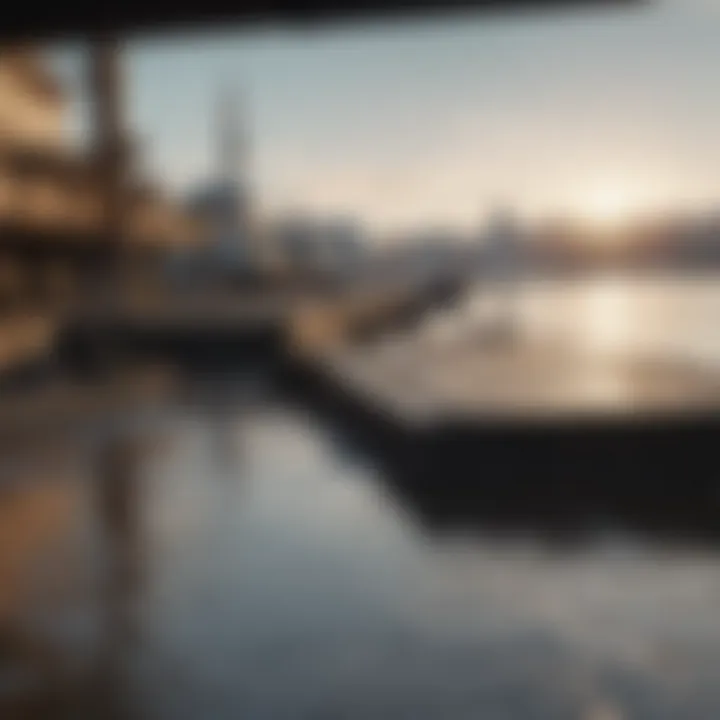
Intro
Every dock, whether for personal use or for business, has a shelf life influenced by many factors: weather conditions, materials used, and frequency of usage, just to name a few. Understanding how these elements impact dock repair costs can save owners a boatload of cash in the long run. This guide will walk you through the maze of expenses associated with dock repairs, offering insights that can help not just in budgeting but also in preventative maintenance.
As we dive into the nitty-gritty, we’ll unpack the types of damages that docks commonly face. You’ll find that not all damages are created equal, nor are their associated repair costs. Prices can soar depending on the material composition of the dock and the extent of the damage, making it vital to distinguish between minor wear-and-tear and serious structural deficiencies.
Given the significance of routine inspections and upkeep, this article also seeks to underscore their role in prolonging the lifespan of your dock, ultimately benefiting your wallet.
Let’s start by understanding how the customer demographics can influence repair needs and costs.
Intro to Dock Repair Costs
Dock repair costs can be both a fearsome puzzle and a necessary reality for boat owners and marina operators alike. With fluctuating prices tied to materials, labor, and regional factors, it becomes vital to grasp what the costs involve.
When we kick under the hood—or should I say, under the dock—of these expenses, we're talking about more than just numbers on a bill. Understanding the financial implications behind dock repair costs can lead to informed decisions that save both time and money in the long run. Consider a scenario: A minor crack has formed on your dock. Ignoring it could lead to larger structural failures, which in turn could skyrocket expenses. In this context, being aware of these costs helps not just in budgeting but also in prioritizing maintenance.
Defining Dock Repair Costs
Dock repair costs are multifaceted; they encompass everything from minor cosmetic fixes to significant structural overhauls. There are various elements that contribute to the total cost of repairs. The two major components include:
- Labor Costs: This signifies the expenses associated with skilled workers who will perform the repairs. Their expertise can be the difference between a job done right and a potential disaster.
- Material Costs: The type of materials your dock is made from, and what is needed for repairs will dramatically impact costs. For example, a wooden dock may require different maintenance materials compared to a composite or aluminum dock.
Recognizing these components equips dock owners with the knowledge to foresee costs better. Understanding the details now can potentially avert budget-busting surprises down the line.
Importance of Understanding Costs
Grasping the intricacies of dock repair costs is crucial for several reasons. Firstly, it helps in effective budgeting. When you know how much repairs generally run—along with potential variations—you’re in a stronger position to allocate resources wisely.
Secondly, there’s the aspect of preventative action. An informed dock owner can schedule routine inspections and maintenance tasks, reducing the likelihood of major damage and thus heavy costs later. Understanding costs also aids in making more strategic choices when it comes to hiring contractors or deciding on materials. Opting for quality over euphoric, low-cost solutions often pays dividends in the long run.
"An ounce of prevention is worth a pound of cure."
In essence, acknowledging these costs aids in cultivating a proactive mindset. This ensures that you’re not just reacting to repairs, but planning for them to maintain the dock's longevity.
Common Types of Dock Damage
Understanding the various types of dock damage is crucial for any dock owner. It’s like knowing the ins and outs of your car’s engine; without that knowledge, you can’t keep it running smoothly. Dock damage can range from natural wear to more severe structural issues, each with its own set of implications and repair needs. By recognizing these different issues early, you can stave off significant costs down the line and ensure the longevity of your dock.
Weather-Related Damage
Weather can be a true nemesis when it comes to dock maintenance. Water levels fluctuate, temperatures swing from one extreme to another, and storms can pack a punch. Each of these factors can wreak havoc on your dock’s structural integrity.
For instance, prolonged exposure to rain can lead to rotting wood, while harsh sunlight can dry it out and cause cracking. Similarly, freezing temperatures can expand any trapped water inside materials, leading to further deterioration.
- Key Considerations:
- Regularly check for signs of water intrusion or swelling.
- Use weather-resistant materials when possible; it pays off in the long run.
Investing in protective coatings or shields can help mitigate some of these impacts, extending the life of your dock.
Structural Failures
Structural failures represent a more complex and often costly set of issues. These problems arise when the physical framework that supports your dock begins to fail, usually due to poor design, inferior materials, or lack of proper maintenance. Think of it like a foundation—cracks in the structure can compromise the whole setup.
Common causes of structural failures include:
- Inadequate support systems, leading to sagging.
- Erosion from waves or currents that undermines pylons.
- Faults in the assembly, such as improper bolts or joints that weaken over time.
Addressing these problems early can save you from a full-blown overhaul later. Take it from someone who's learned the hard way: the cost of proactive replacement is usually leaps and bounds cheaper than full reconstruction.
Wear and Tear Over Time
Finally, let’s not overlook the issue of good ol’ wear and tear. This is entirely normal and happens even when your dock seems well-made and well-maintained. With everyday use, components of your dock can begin to fray or degrade—just like the tires on your vehicle.
- Common signs of wear include:
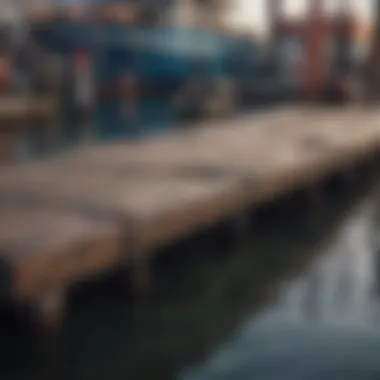
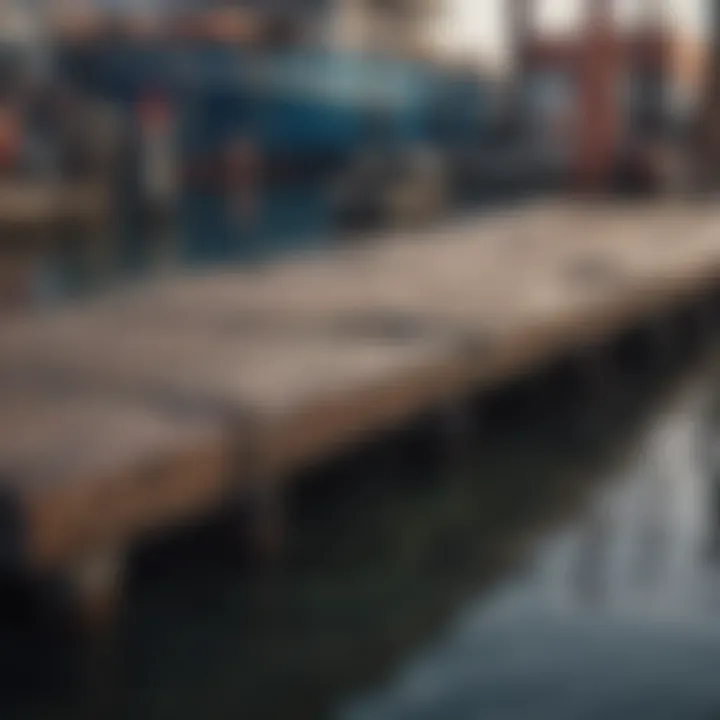
- Splintering wood
- Loose fittings or hardware
- Rusted metal components
Understanding these signs helps you gauge when it’s time for simple fixes versus when you might need full replacements. A standard recommendation include conducting seasonal inspections to evaluate the dock's condition, ensuring you catch any issues before they escalate.
Remember, a stitch in time saves nine. Tackling minor issues early can prevent them from snowballing into major expenses.
Factors Influencing Repair Costs
Understanding the factors that influence dock repair costs is crucial for any dock owner looking to maintain their investment effectively. Different elements play a pivotal role in shaping the overall cost, and being familiar with them can save you some serious cash in the long run. Let’s break it down into three significant aspects: material selection, labor costs, and the location of the dock.
Material Selection
When it comes to dock repairs, the choice of materials can make or break your budget. There’s a vast array of options, from treated lumber to composite materials and even aluminum. Each one has its pros and cons. For instance, while treated wood is often cheaper upfront, it might not have the same longevity as PVC or composite materials.
- Treated Wood: Generally economical, but susceptible to rot and wear from marine elements.
- Composite Materials: More expensive but resistant to weather and requires less maintenance over time.
- Aluminum: Lightweight and durable, however, installation costs can be higher.
If you skimp on materials, you could end up paying twice when repairs become necessary sooner than expected. Choosing something durable is like buying peace of mind for your dock.
Labor Costs
Labor costs are another major factor impacting repair expenses. The rates can vary dramatically based on several factors:
- Experience of the Workers: Skilled labor comes at a premium, but may also lead to more efficient and higher quality work. It's like choosing an ace mechanic; they might charge more, but the job gets done right the first time.
- Time Factors: Depending on the extent of the repairs, the longer the job takes, the more it will cost. Don't forget the cost of downtime—when the dock is out of commission, revenue might be lost if it's a rental or commercial space.
- Location and Accessibility: If your dock is challenging to reach, such as being on a remote island or in a location with difficult access, that will certainly inflate labor costs.
Location of Dock
Finally, the location of your dock plays a significant role in determining repair costs. Here’s why:
- Marine Environment: Docks situated in saltwater areas may suffer corrosion and structural issues faster than those in freshwater regions. Salt eats away at materials, leading to more frequent repairs.
- Weather Patterns: Areas with harsh weather conditions may demand more resilient materials and rigorous maintenance schedules. If you’re in a location that’s sunny one moment and stormy the next, you might need to factor in additional wear protection.
- Regulatory Considerations: Some locations have strict environmental regulations that can affect your repair options and costs. Understanding the local laws is essential so you don’t face penalties or need additional permits during repairs.
Keeping these factors at the forefront of your planning can significantly lower your repairs costs over time.
By taking the time to carefully weigh each of these elements, dock owners can ensure they make informed decisions that impact their budgets and the longevity of their docks.
Estimating Dock Repair Costs
Estimating dock repair costs is not just a mere calculation; it's truly an art form that requires a healthy dose of intuition and experience. Understanding the costs involved is crucial for anyone looking to manage their dock effectively. Cost estimation allows dock owners to navigate expenses more fluidly, transforming what could be a cumbersome process into a well-oiled operation.
Knowledge of these costs can help prevent financial headaches down the road. After all, docking and repairs can become a black hole for money if not managed properly. Thus, grasping how to estimate these expenses can benefit significantly, allowing for proactive maintenance rather than reactive repairs.
Conducting Initial Assessments
The first step to pinning down repair costs is conducting a thorough initial assessment. This stage is all about taking stock of the situation. Look over every inch of the dock to uncover damages, both obvious and subtle.
- Visual Inspection: Begin with a visual inspection; walk around and search for cracks, leaks, and any loose or wrinkled materials. Keep an eye out for bubbled paint or rotting wood, signs that tell a story of decay.
- Documentation: Document everything with photographs. This creates a timeline you can refer back to and helps professionals gauge the extent of the work needed.
- Cost Estimation Tools: Consider using cost estimation tools or software designed specifically for dock repairs. They can help you get a ballpark figure that can guide your next steps.
Taking the time to assess the condition of the dock can pay off handsomely. It not only reveals potential problems waiting to rear their ugly heads but can also ease the unexpected shocks that often accompany larger repair bills.
Utilizing Professional Appraisals
Sometimes, a trained set of eyes is needed to unearth the full extent of the damages. This is where professional appraisals come into the picture. Experts can assess not just the visible damages but also underlying issues that might go unnoticed.
- Expert Opinions: Getting an expert appraisal can be invaluable. They routinely recognize patterns that the average owner might miss, such as root causes of wear-and-tear.
- Itemized Reports: A good contractor will provide an itemized breakdown of repairs, materials, and labor, making the estimation process clearer and more manageable.
- Future Considerations: Additionally, professionals often have insights about future repairs, factoring in ongoing maintenance, which is crucial for long-term budgeting.
Seeking a professional appraisal can save dock owners from undergoing a financial rollercoaster later on. It may come with a cost initially, but the insights and information are worth their weight in gold. From identifying potential pitfalls to providing a comprehensive overview of needed repairs, professional assessments are indispensable in the journey of estimating dock repair costs.
"An ounce of prevention is worth a pound of cure."
In the end, understanding how to accurately estimate dock repair costs arms owners with the exceptional knowledge needed to make informed decisions, turning what initially appears daunting into a manageable task.
Budgeting for Dock Repairs
Budgeting for dock repairs is a critical component for dock owners looking to maintain their investment. When you think about it, docks can be quite the financial commitment. If not properly budgeted, repair costs can quickly spiral out of control, leaving dock owners in a lurch. Establishing a solid budget helps in navigating through repair processes with a clearer financial roadmap. Not only does it shield against unforeseen expenses, it allows dock owners to prioritize maintenance tasks, ensuring longevity and safety.
Setting a Realistic Budget
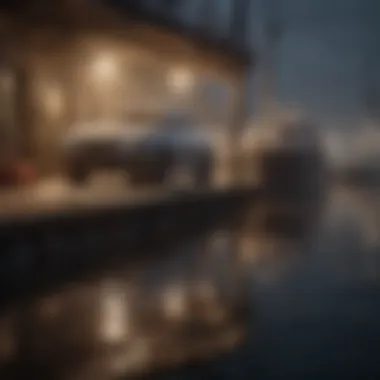
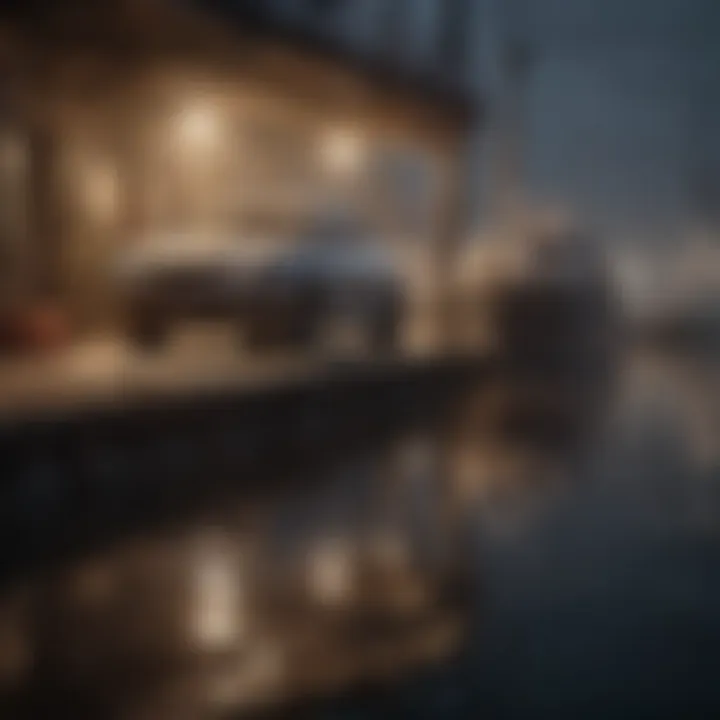
Crafting a realistic budget starts with a thorough understanding of potential repair needs. First off, owners should conduct a comprehensive assessment of the dock’s current condition. This involves examining all components, from the surface to the structural supports. After identifying necessary repairs, it’s wise to consult industry resources to gauge common costs associated with various types of damage. Engaging experienced contractors can also offer insight into labor pricing.
Here's a step-by-step approach to set that budget:-
- Evaluate Recent Repairs: Reflect on past repair expenses. This gives a clue about costs that might crop up in the future.
- Research Material Costs: Materials vary greatly in price and durability. Quality might come with a hefty price tag, but investing wisely could save money in the long run.
- Consider Maintenance Frequency: Regular maintenance often leads to lower repair costs over time. The budget should account for routine checks.
- Flexibility: Be prepared to tweak your budget as new information surfaces through assessments.
By following these guidelines, dock owners can avoid underestimating the expenses that go with upkeep, which is a common pitfall. An accurate budget not only reduces stress but also increases overall satisfaction when it comes to dock management.
Accounting for Unexpected Costs
When it rains, it pours, or so they say. Keeping that in mind, it's essential to factor in those unexpected costs that seem to pop up out of nowhere. Even with a well-thought-out budget, surprises can occur. Natural disasters, wear and tear, or even sudden changes in the local environment could lead to repairs that are entirely unanticipated.
To handle these unexpected incidents, consider the following:
- Emergency Fund: Set aside a portion of your budget as a buffer against surprises. Generally speaking, allocating about 10 to 15% for emergencies is prudent.
- Insurance Review: Make sure to have adequate insurance coverage. Knowing what is covered can ease financial strain when unexpected repairs arise.
- Seasonal Impact: Certain times of year can lead to more damage, particularly in regions susceptible to severe weather. Staying aware of seasonal conditions can help predict and plan for repairs.
"Budgeting isn't just about limiting what you can spend, but about understanding the full picture of what that investment entails."
By being proactive rather than reactive, dock owners can navigate through potential financial hiccups, giving peace of mind as they enjoy their waterfront property.
Preventative Maintenance for Docks
Preventative maintenance is not just a checklist to complete; it's an ongoing commitment to the longevity and safety of your dock. Think of it as a health regimen for your dock—much like how a vehicle or any other significant investment requires regular checkups and tune-ups, so does your dock. By keeping a vigilant eye on its condition, you can catch potential issues before they snowball into expensive repairs.
Firstly, regular inspections are essential. Skipping routine checks might seem like a small oversight, but it can lead to major mishaps down the line. With unpredictable weather patterns and corrosive marine environments, your dock faces numerous risks daily. Performing inspections every few months allows you to spot early signs of wear or damage, which in turn can save you a small fortune. From soft spots in the decking to rust on metal components, a little vigilance goes a long way.
Consider the benefits of these inspections:
- Preventing Major Repairs: Catching small problems early means addressing them before they escalate.
- Increase Safety: A well-maintained dock minimizes hazards for users, thus reducing liability.
- Enhance Property Value: A well-kept dock can significantly contribute to the overall value of your property.
Regular Inspections and Maintenance Checks
Implementing a routine maintenance schedule helps to establish a pattern of care. This does not require a lot of time or excessive resources but can be done simply with a diligent approach. Each time you inspect, look for signs that indicate wear and tear. Typical checks might include assessing:
- The stability of pilings and supports
- The condition of the decking material
- Any visible signs of water damage or mold
- Corrosion on metal fittings and components
Taking thorough notes during these inspections is helpful. Not only does it keep your maintenance history documented, but it also provides insight into any recurring issues that need addressing. [quote] "An ounce of prevention is worth a pound of cure."
Investing in Quality Materials
One of the smartest moves a dock owner can make is to invest in quality materials from the get-go. While you might be tempted to cut corners with cheaper options, they can lead to a false economy. Lower-quality materials may indeed have a lower upfront cost, but they often come bundled with higher repair and replacement expenses over time.
Durable materials like marine-grade aluminum, hardwoods, or composites are designed to withstand harsh conditions.
Consider the following when choosing materials:
- Durability: Select materials that are resistant to rot, corrosion, and UV exposure.
- Long-Term Cost: Calculate the total cost of ownership; how long the materials will last versus how often they will need to be replaced.
- Environmental Impact: Be mindful of materials that not only serve well structurally but are also eco-friendly.
By taking these tips into consideration and staying proactive, you’re setting your dock up for extended serviceability, ensuring that it remains a safe and useful asset for years to come.
The Role of Contractors in Dock Repairs
When it comes to maintaining and repairing docks, the role of contractors can't be overstated. These professionals are not just hired hands; they are skilled experts who can make a significant difference in the quality of repairs and overall dock longevity. Selecting the right contractor ensures that repair costs remain manageable while still achieving the highest standards of work.
Selecting a Qualified Contractor
Finding a good contractor for dock repair means more than just picking a name out of a hat. It requires some legwork and due diligence. To start, it's wise to look for contractors who specialize in marine construction and have verifiable experience in dock repairs. This niche skill set often brings a deeper understanding of the marine environment and its specific challenges.
- Check Reviews and Portfolios: Look at past projects and read client testimonials. Satisfied customers can provide insights into a contractor's reliability and quality of work.
- Request Certifications: Always inquire about any relevant certifications. This shows that the contractor has met specific standards in their trade.
- Legal Considerations: Make sure that the contractor is licensed and insured for marine work. This protects you from any liability in case of accidents during the repair process.
Choosing a qualified contractor helps mitigate unforeseen issues during repairs and could even save you money in the long run. An experienced contractor knows how to maximize the lifespan of materials used and can often identify potential problems before they become severe.
Understanding Contractor Pricing Models
Once you have sifted through the candidates and selected a few contractors, the next step is to understand their pricing structures. Different contractors may have various models for charging, and being aware of these can help you keep your budget on track.
- Hourly Rates vs. Flat Fees: Some contractors charge hourly rates, meaning you’ll pay for the time they spend working. Others may give you a flat fee for the entire job, which can help avoid surprise expenses. Always clarify this early on.
- Materials Costs: Understand if the quoted price includes all materials or if you will need to procure some yourself. Some contractors might mark up material costs, which could affect your overall expenses.
- Contingency Planning: Ask contractors how they handle unexpected costs. It is not unusual for repair tasks to reveal deeper underlying problems, so having a clear understanding of their approach to additional charges is crucial.
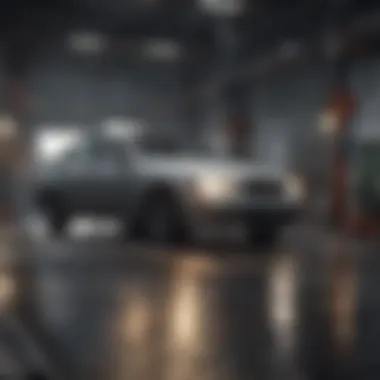
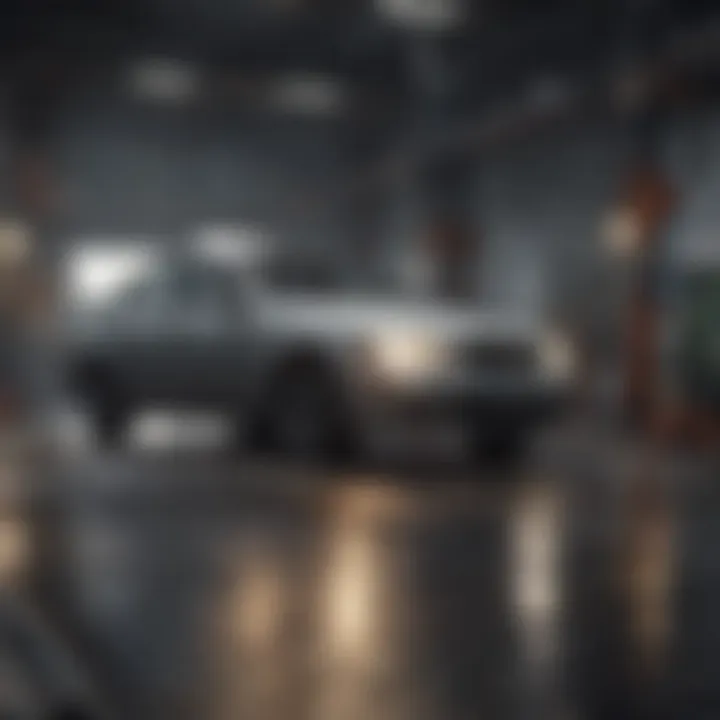
"Investing time up front to find the right contractor is akin to paying for an insurance policy against costly mistakes down the line."
Navigating through these pricing models with awareness allows you to plan better for dock repairs. Good communication with your contractor will set expectations straight and relieve potential stress over finances during the repair process.
Case Studies: Comparing Repair Costs
When it comes to dock repairs, the adage "what you see is what you get" rarely holds true. Repair costs can vary wildly based on numerous factors. That’s where case studies come in handy. They present real-life scenarios that illuminate the complexities involved in dock repairs. By analyzing specific examples, dock owners can gain valuable insights into expected costs, potential pitfalls, and best practices. This section will dive deep into the critical elements surrounding the comparison of repair costs, allowing for a clearer understanding of what influences these figures.
Analyzing Small-Scale Repairs
Small-scale repairs often involve minor wear and tear, like replacing a few planks or reinforcing a leaning post. These repairs typically appear less daunting on the surface, often leading to underestimation of their impact. However, neglecting these issues can snowball into larger problems. For instance, consider a dock that requires replacement of several boards due to rot. The cost might seem reasonable initially at about $500 to $1,000, covering materials and labor.
Benefits of Analyzing Small-Scale Repairs:
- Cost Awareness: Understanding the cost associated with small fixes allows for efficient allocation of budgets.
- Timeliness: Acting promptly on small repairs can prevent escalation into larger, more costly issues.
- Preventative Insight: Knowing common small-scale problems helps in scheduling regular maintenance checks.
"A stitch in time saves nine." This proverb rings especially true in the context of dock repairs, where small issues can quickly snowball if left unattended.
Examining Major Overhauls
Major overhauls, on the other hand, involve comprehensive renovation projects. These might include complete dock reconstruction or significant structural upgrades. The costs associated with such projects can skyrocket, often ranging from $10,000 to $50,000 or more, depending on materials used, design intricacies, and labor costs.
In examining a case where a dock faced extensive damage from a storm, the owners opted for a major overhaul that involved replacing not just the decking, but also the pilings and supports. This project required various permits and multiple contractors, which added layers of complexity and, ultimately, cost.
Considerations for Major Overhauls:
- Material Quality: The better the material, the longer the lifespan of the repair, but this also increases initial costs.
- Contractor Selection: Choosing the right contractor can make a world of difference in both quality of work and overall cost efficiency.
- Project Timeline: Major overhauls can take time. Budgeting for delays is crucial to avoid financial strain.
In summary, the comparison of repair costs through case studies provides a unique lens into the operational realities of dock maintenance. By understanding both small-scale and large-scale repair scenarios, dock owners can navigate the murky waters of repairs with more confidence and strategic foresight.
Impact of Dock Location on Repair Costs
Effects of Marine Environment
The marine environment can wreak havoc on your dock if you’re not careful. For instance, if your dock is situated in a saltwater area, you might find yourself facing frequent corrosion issues. Saltwater tends to eat away at materials like metal and wood more aggressively than freshwater. It’s not just the water itself, but the waves, tides, and weather phenomena like storms can take a toll too.
Moreover, factors such as the type of marine life in the area can add to repair costs. Barnacles, seaweed, and other organisms can attach themselves to the dock, leading to additional wear and tear. You may have to spend extra on cleaning and maintenance efforts that you wouldn't face in a less active environment. Regular inspections and targeted treatments depending on your specific conditions can sometimes forestall more considerable expenses down the line.
“A stitch in time saves nine,” as the old saying goes. Taking proactive measures in marine environments can save you significant funds in the long run.
Accessibility Issues
How easy or difficult it is to access your dock can also have a major impact on repair costs. If your dock is located in a remote area, bringing in heavy machinery or materials can become quite the ordeal. Transport costs can skyrocket, eating into your budget significantly. In contrast, docks that are easily accessible allow for more competitive pricing on materials and labor since contractors can reach the site without any fuss.
Additionally, if repairs require diving or specialized equipment due to the dock’s location—like at the end of a lengthy pier or in deeper waters—the costs can increase substantially.
Here are a few considerations regarding accessibility:
- Proximity to Suppliers: Are your material suppliers close by, or will you need to pay high shipping costs?
- Ease of Contractor Access: Can contractors swiftly bring in their equipment, or will they be delayed by difficult logistics?
- Underwater Conditions: Accessibility underwater can affect what kind of repairs can be performed and how quickly.
Ultimately, understanding the unique challenges posed by your dock's location is key. By factoring in these elements at the planning stage, you can position yourself to better manage costs and avoid unexpected financial strain.
Closure: Strategic Approach to Dock Repair Costs
Taking a strategic approach to dock repair costs is crucial as it encompasses various aspects from budgeting to maintenance strategies. Understanding the financial implications of dock ownership is not just about knowing how much repairs will set you back, but also about anticipating needs and creating a financial cushion for the future.
In this context, adopting a strategic mindset means being proactive rather than reactive. It emphasizes the importance of preparing for eventualities like material wear, environmental challenges, and even labor cost fluctuations. This foresight can significantly reduce stress during unexpected repairs, as you’ll already have mechanisms in place to handle these challenges before they become severe issues. Ultimately, a strategic outlook has the potential to save boat enthusiasts and dock owners a tidy sum over time.
Summarizing Key Takeaways
Several essential points emerged from our deliberations on dock repair costs:
- Know Your Dock: Regular assessments and understanding your dock's unique needs can proactively prevent small issues from escalating into larger, more costly repairs.
- Budgets and Reserves: Establishing a clear budget and maintaining reserves for unexpected costs is fundamental. An emergency fund can keep your dock functional without financial strain.
- Quality Materials: Investing in high-quality materials often pays off in the long run; they withstand wear and tear better, reducing the frequency and extent of repairs.
- Professional Help: Engaging skilled contractors can make a world of difference in the quality of repairs. They can offer insights that prevent future issues, ensuring your dock remains in good shape.
- Regular Maintenance: Routine inspections and maintenance minimize repair needs and extend the lifespan of your dock. This preventive approach is the most cost-effective measure you can take.
In sum, being armed with knowledge and a plan is the best way to navigate the sometimes murky waters of dock repair expenses.
Encouraging Proactive Maintenance Practices
Encouraging proactive maintenance practices goes beyond just paying lip service to the idea. It requires a commitment to regular upkeep and an understanding of your dock's environment. Here are some effective practices:
- Conduct Regular Inspections: Schedule periodic inspections to identify wear and tear. Look for rotting wood, rust, or structural issues that might require attention. Issues caught early can often be addressed at a fraction of the cost.
- Establish Maintenance Protocols: Create a detailed maintenance schedule outlining necessary tasks such as cleaning, sealing, and checking for damages. Following a protocol can help you stay organized and proactive.
- Invest in Upkeep Supplies: Stock up on necessary maintenance supplies such as paints, sealants, and cleaning tools. When you keep these supplies on hand, you'll be less likely to procrastinate those minor repairs.
- Educate Yourself: Take some time to understand the materials used in your dock and their care requirements. Knowledge is power, and knowing what to do can save you money.
- Collaborate with Experts: Form partnerships with local contractors or dock maintenance professionals. Regularly consulting with them can provide valuable insights into maintaining your dock’s health.
By fostering these proactive maintenance practices, you can protect your investment and extend the lifespan of your dock, making it a resilient structure for years to come. The end game is to not only keep costs down but also maximize the enjoyment of your time on the water.