Exploring Rotationally Molded Polyethylene in Automotive
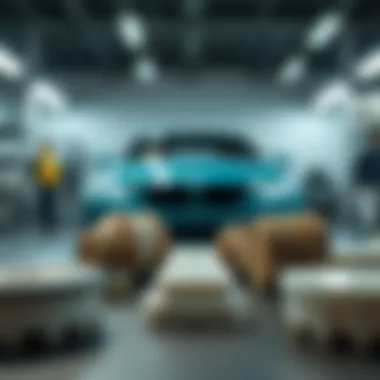
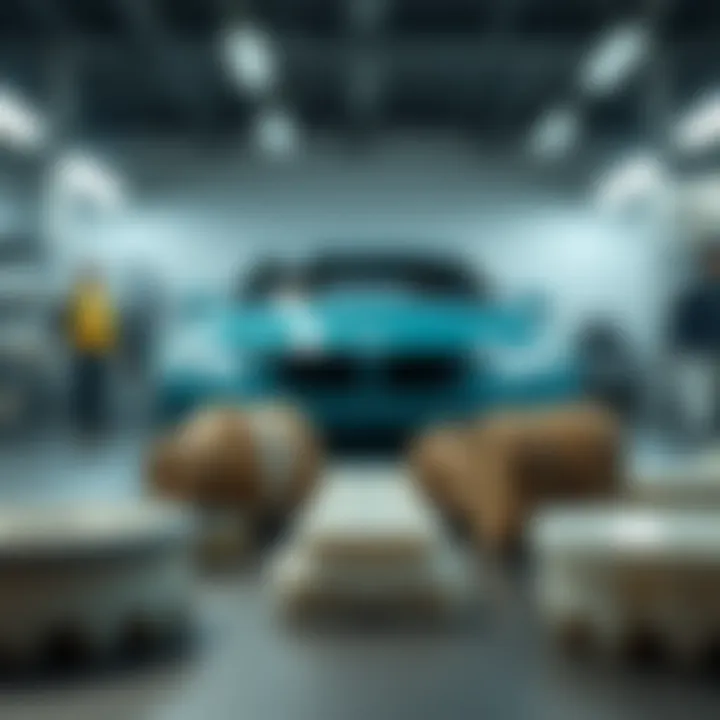
Intro
Rotationally molded polyethylene, a material that might not be the first thing that springs to mind when discussing automotive applications, has carved out a niche for itself in recent years. This is not just a passing fad; rather, it’s a testament to the material’s unique properties and versatility. The automotive industry, always in search of materials that can withstand the rigors of real-world usage while also being cost-effective, has found a reliable ally in this type of polyethylene. As we delve deeper into this analysis, we’ll uncover how this engineering marvel is shaping the future of vehicle design and performance.
Customer Segmentation
When discussing market trends in automotive applications, it’s crucial to understand who the consumers are. In the context of rotationally molded polyethylene, customer segmentation can reveal insightful trends.
Demographic Insights
The demographic landscape is not a one-size-fits-all scenario. Typically, buyers range from automotive manufacturers focusing on sustainability to individual vehicle enthusiasts keen on performance upgrades. Age factors considerably—most customers are in the 25-55 age range. This group tends to be more tech-savvy and environmentally conscious, often influenced by the increasing push towards green initiatives in automotive engineering.
Behavioral Patterns Among Buyers
Understanding the behavioral tendencies of these demographic groups can be revealing. For instance, many buyers are proactive in researching materials before making purchases. Decisions are influenced by practicality and aesthetic appeal, where rotationally molded polyethylene often stands out due to its durability and lightweight nature. Sustainability is a hot-button issue, with many buyers opting for materials that are recyclable and environmentally friendly. People value transparency and often gravitate toward brands that highlight their commitment to sustainable practices.
In-Depth Product Analysis
Now, let’s turn our lens toward a more detailed examination of rotationally molded polyethylene's applications within the automotive sector. This level of analysis helps to synthesize insights that can guide both manufacturers and consumers alike.
Performance Assessment
Performance is the name of the game in the competitive automotive market. Rotationally molded polyethylene measures up exceptionally well. Its resistance to impact and stress means that components made from this material can endure the bumps and bruises that come with daily driving. Additionally, the ability to create complex shapes without the need for excessive assembly gives manufacturers a valuable edge, reducing time and labor costs. A well-crafted polyethylene part is not merely about strength; factors like UV resistance and temperature tolerance further enhance its appeal.
Owner Satisfaction Surveys
Feedback from vehicle owners often reveals crucial tidbits of information about their satisfaction with various materials used in their vehicles. Surveys indicate that owners utilizing vehicles with rotationally molded polyethylene components often highlight enhanced durability and lower maintenance needs. They frequently mention aspects like lighter weight contributing to improved fuel efficiency—a particularly attractive feature for many in today’s market. To underscore the viability of this material, consider the quoted satisfaction scores from recent owner surveys, which often land in the realm of 85% to 90% for performance-related satisfaction.
"Durability is king in automotive, and the weight savings from rotationally molded polyethylene helps keep our rides efficient without compromising on quality!"
Prelude to Rotationally Molded Polyethylene
The automotive industry constantly seeks materials that can enhance performance, reduce costs, and ensure durability. Rotationally molded polyethylene stands out as a pivotal choice for manufacturers, offering a unique blend of properties advantageous for various applications. This introduction lays the groundwork for understanding this material's significance in automotive engineering, focusing on its specific advantages and considerations.
Definition and Overview
Rotationally molded polyethylene is a thermoplastic process that shapes plastics into hollow parts. The process involves heating the plastic resin in a mold and then rotating the mold on multiple axes. This unique technique leads to a smooth, uniform, and thick product with minimal wastage. For automotive applications, it provides flexible component designs and the potential for integrated features in one piece, streamlining both production and assembly processes. The ability to create complex shapes without requiring intricate tooling is valuable in this fast-paced industry. This leads to lower production costs and faster turnaround times, making it ideal for automotive parts.
Historical Context
The journey of rotationally molded polyethylene in the automotive world is quite fascinating. Historically, the method gained traction in the 1960s and 1970s, initially being favored in the production of items like kayaks and playground equipment. Over the years, it transitioned into the automotive sector as manufacturers sought more versatile materials to meet evolving needs. Its applications expanded, particularly in exterior and interior components, as companies recognized its potential for greater durability and design flexibility.
Over the decades, as vehicle designs became more complex, the adaptability of rotationally molded polyethylene allowed engineers to explore innovative applications, such as integrated storage solutions and custom dashboard elements. Today, its controllable properties and lightweight nature help meet contemporary challenges, making it a staple in automotive materials.
Whether it’s the evolution from basic designs to cutting-edge functionality or the material's ongoing relevance in the face of emerging technologies, the importance of recognizing rotationally molded polyethylene within the automotive sector cannot be overstated.
Understanding the Manufacturing Process
The manufacturing process of rotationally molded polyethylene is a crucial component of its application in the automotive sector. This aspect not only determines how the product is made but influences its quality, cost, and overall effectiveness in meeting industry standards. Understanding these processes offers insights into potential benefits, challenges, and suitability of rotational molding for various uses in vehicles. By digging into the nitty-gritty of the manufacturing steps, we can appreciate how this method aligns with modern-day demands of durability and efficiency in automotive design.
Basics of Rotational Molding
Rotational molding involves a unique approach to shaping polyethylene through a heating and cooling cycle. This method is particularly advantageous for making hollow parts, thanks to its ability to provide uniform wall thickness and excellent strength properties. It starts with a predetermined amount of powdered resin placed in a mold, which is then heated and rotated. This rotation facilitates even distribution of the resin while it melts, forming a seamless product. The simplicity of this method eliminates the need for complex tooling like other manufacturing processes might require, making it a go-to choice for many automotive applications.
Material Selection
Choosing the right material is pivotal in the rotational molding process. Polyethylene, especially high-density polyethylene, is favored for its strength-to-weight ratio and resistance to impacts and chemicals. The selection criteria are based on the end-use of the products: for instance, interior components of vehicles might focus more on aesthetic qualities and durability, while exterior parts might prioritize weather resistance. This tailored approach to material selection enhances performance attributes, ensuring the final product meets the specific demands of automotive applications.
Key Stages of Production
Delving into the production process reveals several critical stages. Each of these steps plays a significant role in determining the quality and functionality of the molded products.
Mold Design
Mold design is one of the foundational elements in the production of rotationally molded polyethylene products. An effective mold can drastically affect the outcome of a design, influencing the material's distribution and the final product's structural integrity. Key characteristics of molds include their thermal conductivity and the ability to achieve nominal wall thickness.
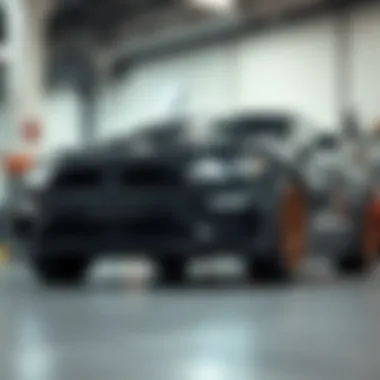

The design also offers significant flexibility, allowing for intricate shapes and features that can be hard to replicate through other fabrication methods. This is particularly beneficial because automobiles often require tailored components that adhere to specific dimensions and curves. However, creating high-quality molds can involve substantial upfront costs and lead times.
Heating Process
The heating process in rotational molding is vital for achieving the desired melting of the polyethylene resin. During this stage, molds are typically heated in an oven where the resin reaches its softening point. This process is crucial because overheating can lead to degradation of material properties, while insufficient heating may result in weak bonding within the molded product. The way heat is applied can also vary, with options like conduction and convection, each having its advantages.
A notable advantage of proper heating management is the ability to produce items with uniform densities, which has significant implications for durability in automotive applications. However, one must manage energy consumption to keep production costs in check.
Cooling Techniques
Finally, cooling techniques play a significant role in solidifying the molded polyethylene parts. Adequate cooling ensures that the shape is retained and that any stress within the material is minimized. Cooling can be achieved through air or water, depending on the production scale and the thermal properties desired in the final product. A key characteristic of this stage is that quicker cooling can lead to more efficient production cycles, yet it must be carefully controlled to prevent warping or cracking.
The advantage of having well-implemented cooling strategies means products can be produced faster while ensuring structural integrity, vital for automotive components subjected to rigorous wear and tear.
In summary, each stage involved in the manufacturing of rotationally molded polyethylene comes together to create a process that echoes cost-effectiveness, flexibility in design, and durability—all of which are paramount in the automotive industry.
Properties of Rotationally Molded Polyethylene
Understanding the properties of rotationally molded polyethylene is vital to grasp its significance in automotive applications. This material isn't just a choice out of convenience; it's a powerhouse of attributes that offer specific advantages in numerous automotive contexts. Let's take a closer look at each critical aspect that makes polyethylene stand out.
Physical Characteristics
Density
Density plays a pivotal role in defining the performance of polyethylene-based components. With densities generally ranging from 0.91 to 0.96 g/cm³, this lightweight material contributes to overall fuel efficiency by reducing vehicle weight. Lower density means lighter parts, which can translate into better miles per gallon (MPG).
A key characteristic of density here is its influence on maneuverability and speed. A lighter vehicle can accelerate faster, making the driving experience more enjoyable. However, while many may appreciate the positive impact of reduced weight, one must also consider that an excessively low-density polyethylene might compromise overall durability, especially under heavy loads.
Unique Feature: In cases where manufacturers need balance—flexibility with robustness—density plays a deciding role. As automakers push for innovation, they often experiment with density variations to optimize the performance of specific parts.
Thermal Resistance
Thermal resistance is another indispensable property of rotationally molded polyethylene. This material exhibits high thermal stability, allowing it to withstand temperatures from around -40 to 80 degrees Celsius without significant deformation. This attribute is crucial for automotive applications, where parts often face extreme weather conditions.
The primary benefit of high thermal resistance lies in its role in providing stability and longevity to automotive components. A dashboard or a bumper made from this material remains intact despite seasonal changes, ensuring not just aesthetics but also safety for drivers and passengers.
Unique Feature: The resistance to thermal fluctuations also ensures that no harmful substances leach into the interior of the vehicle, a significant advantage for consumer safety and environmental integrity.
Impact Strength
When it comes to automotive safety, impact strength cannot be overstated. Rotationally molded polyethylene is revered for its excellent impact resistance, typically enhanced through physical foam structures or additives that bolster its resilience. This characteristic is particularly beneficial when it comes to external components like fenders and bumpers, which are often the first to absorb shock during accidents.
The highlight of impact strength lies in its ability to minimize damage during collisions. When other materials might crack or shatter, polyethylene absorbs energy. This not only protects the parts but can potentially save lives by reducing the amount of force transmitted to the vehicle’s occupants.
Unique Feature: This durability creates a lasting impression on manufacturers who seek longevity in their vehicle components, as well as a competitive edge over models made from traditional materials like metals.
Chemical Resistance
Chemical resistance is paramount in automotive environments where components are exposed to oil, gasoline, and other corrosive substances. Rotationally molded polyethylene resists these chemicals exceptionally well, allowing manufacturers to design parts with confidence. The material’s ability to withstand these harsh conditions means its lifespan is markedly extended, reducing replacement costs over time.
This characteristic does not merely protect the vehicle; it also enhances overall environmental safety. By preventing leaks or failures, vehicles can operate more efficiently and with less environmental impact, which aligns with an increasing focus on sustainability in the automotive industry.
Color and Finish Options
Aesthetics might not be the primary concern when discussing material properties, but they shouldn't be ignored. Rotationally molded polyethylene offers a variety of color and finish options, allowing for creative influences in automotive design. Whether a matte finish or a glossy sheen, manufacturers can achieve visually appealing results that remain durable against wear and tear.
Moreover, uniformity in color means that defects are less visible, which enhances the perceived quality of the vehicle. Different textures can also contribute to anti-slip surfaces, improving functional attributes while appealing to consumers' design preferences.
In summary, the diverse properties of rotationally molded polyethylene make it an invaluable asset in automotive applications. By understanding density, thermal resistance, impact strength, chemical resistance, and aesthetic options, automotive innovators can harness its full potential to create vehicles that are safer, lighter, and visually appealing.
Applications in the Automotive Industry
Rotationally molded polyethylene has found its niche in the automotive landscape, serving various purposes that enhance both functionality and aesthetics. From interior design elements to rugged exterior parts, its versatility and distinctive characteristics elevate the manufacturing process. This section elaborates on the specific roles and advantages that rotationally molded polyethylene fulfills in the automotive industry, presenting a blend of design, utility, and durability.
Interior Components
Dashboard Elements
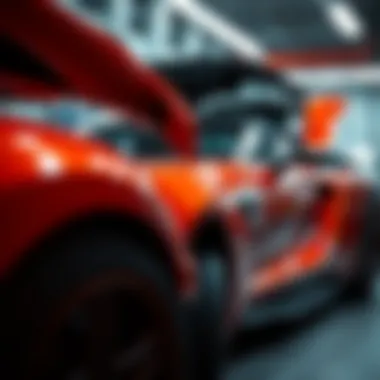
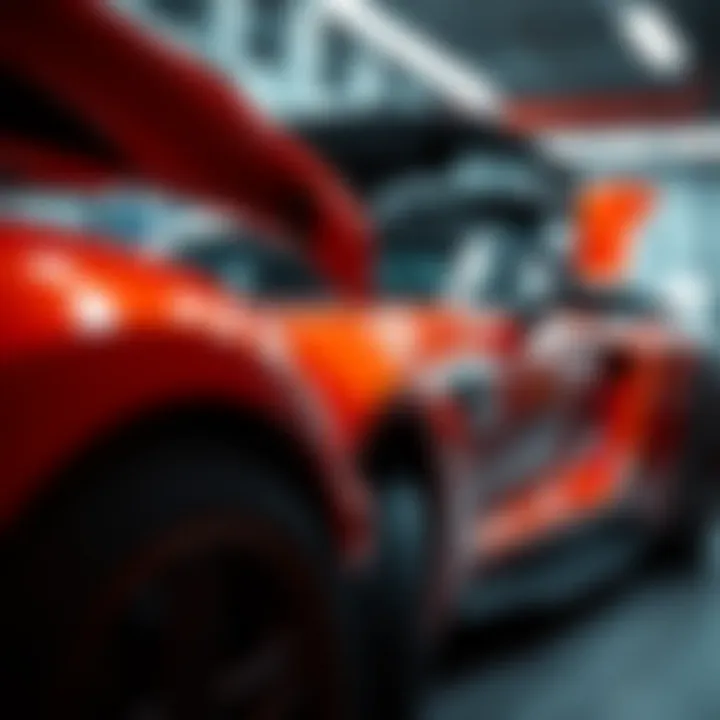
The dashboard is the nerve center of any vehicle's interior. Rotationally molded polyethylene is shaping this essential component in ways that maximize functionality and style. Its lightweight yet tough structure allows for intricate designs without the weight penalties seen in traditional materials. A fascinating aspect of these dashboard elements is their ability to absorb shocks – an essential feature that enhances driver safety during unexpected situations.
The key characteristic of rotationally molded dashboards is their seamless construction, which eliminates joints and seams. This not only allows for greater design flexibility but also enhances the dashboard's resistance to dust and dirt accumulation. Another unique feature is the ease of coloring; manufacturers can achieve vibrant aesthetics customized to brand specifications. In terms of advantages, such dashboards can endure strong sun exposure without warping or fading. However, knocks or heavy impacts can damage more easily than metal or composite alternatives, highlighting one of its notable drawbacks.
Storage Solutions
In practical terms, storage solutions within vehicles are paramount, especially for families or adventure-seekers. Here, rotationally molded polyethylene stands out thanks to its high resistance to impact and environmental conditions. Trunks and compartments crafted from this material can withstand the rough and tumble of daily use.
A noteworthy aspect of these storage solutions is their design flexibility; manufacturers can produce customized sizes to fit vehicle models like the Ford F-150 or Honda CR-V seamlessly. This adaptability allows for creative organization systems that maximize space efficiently, a definite boon for everyday users.
However, while the unique feature of these solutions is their resistance to chemicals and fuels, making them suitable for various items, practical considerations must also be acknowledged. For instance, the weight may be overly cumbersome for compact models, requiring careful design to keep balance in mind.
Exterior Parts
Bumpers
On the exterior, bumpers made from rotationally molded polyethylene offer quite a few advantages. One significant aspect is their ability to endure minor collisions without shattering, making them an increasingly preferred choice among manufacturers. Their lightweight nature also contributes to improved fuel efficiency, as reduced weight generally enhances vehicle performance.
A critical characteristic of these bumpers is that they can be molded into complex shapes while still maintaining their structural integrity. This property allows for innovation in design that often isn't feasible with metal bumpers. A unique feature is the potential for integrated attachment points for sensors and cameras, which play a crucial role in modern driving assistance technologies. However, one disadvantage could include vulnerability to extreme UV exposure over time, which may result in surface degradation if not properly treated.
Fenders
Fenders face the brunt of road debris and environmental conditions, making their material choice vital. Rotationally molded polyethylene provides a flexible yet tough solution for modern vehicles. The specific aspect of fenders from this material is their resistance to rust, which is a common enemy for metal fenders. This trait significantly extends their longevity, especially in diverse climates.
The key characteristic that sets these fenders apart is their capacity for customization; they can be tailored to fit various models or provide aesthetic accents for sportier designs. Furthermore, their ability to absorb vibrations reduces noise while driving, enhancing passenger comfort.
Nevertheless, it's important to note the potential for scratches and surface damage; while they are sturdy, prolonged exposure to sharp objects can lead to abrasions. Thus, while rotationally molded polyethylene's fenders have much to offer, it still elicits considerations about overall durability and maintenance.
Storage Systems for Vehicles
Storage systems for vehicles are essential, ensuring that essentials are organized while preventing clutter. Utilizing rotationally molded polyethylene in these systems allows manufacturers to create shapes and compartments that fully utilize available space. Given the variety of models in today's market, ensuring compatibility and maximization of trunk or cargo area is critical.
Rotationally molded polyethylene lends itself well to waterproof solutions, allowing these systems to hold items without fear of moisture damage. For instance, kayak rollers or off-road vehicle racks made from this material excel in both protection and user convenience. However, while the systems they support thrive in performance, they may still face limitations against extreme static weight when overly loaded. At the end of the day, rotationally molded polyethylene’s adaptability ensures innovative and practical storage solutions can evolve alongside consumer needs.
Advantages of Rotationally Molded Polyethylene
Rotationally molded polyethylene stands out as a material of choice in automotive applications due to its unique properties. Understanding these advantages can help manufacturers optimize designs that enhance performance, improve cost efficiency, and extend product lifespan. Let's dive into the specifics of its benefits:
Cost-Effectiveness
When considering automotive manufacturing, cost savings are often at the forefront of decision-making. Rotationally molded polyethylene offers significant cost advantages compared to traditional processes. The tooling costs for molds in rotational molding are generally lower, allowing for smaller production runs without breaking the bank. Since the process can produce complex shapes in one piece, manufacturers can also avoid the need for additional parts and assembly, which cuts down both time and labor costs.
For example, using a single molded compartment for a vehicle’s storage instead of multiple assembled pieces can streamline production and minimize material wastage.
Design Flexibility
One of the most compelling attributes of rotationally molded polyethylene is its design flexibility. This form of molding enables the production of intricate designs that would be challenging to achieve through other methods like injection molding. The ability to produce large, hollow parts without seams greatly reduces the risk of weak points in the design, leading to more robust components.
Moreover, innovations in the design phase can lead to exciting applications such as ergonomic dashboards or custom storage solutions tailored to specific vehicle models and user needs. With the right design, a single mold can yield various iterations of a part, which is a boon for creative automotive engineers looking to differentiate their products from the competition.
Durability and Longevity
Durability is a critical factor in automotive components, and rotationally molded polyethylene excels in this area. The material exhibits impressive resistance to corrosion and impact, making it an ideal choice for both interior and exterior applications. Due to its inherent resilience, parts made from this material can withstand harsh weather conditions, UV exposure, and even chemical spills.
In practical terms, manufacturers can expect improved lifespan of components such as bumpers or storage cases, providing consumers with confidence that their investments will endure daily wear and tear. Regular maintenance costs can also decrease since the material's strength reduces the likelihood of breakage, ultimately benefitting both manufacturers and consumers alike.
"Cost savings, design flexibility, and durability make rotationally molded polyethylene an invaluable asset in automotive manufacturing—catering to the industry’s evolving demands."
In summary, the advantages of rotationally molded polyethylene have far-reaching implications in the automotive arena. By combining cost-effectiveness with design flexibility and exceptional durability, this material supports innovation and practicality in product development. Its increasing prominence reflects the industry's need for solutions that can stand the test of both time and performance.
Challenges and Limitations
While rotationally molded polyethylene boasts many advantages, it is crucial to acknowledge its challenges and limitations within the automotive sector. Understanding these factors allows automotive engineers, manufacturers, and enthusiasts to make informed decisions. Some drawbacks can influence material selection and overall production efficiency.
Environmental Impact
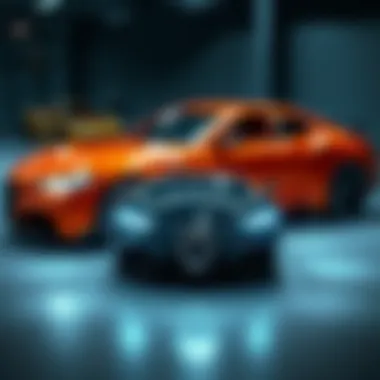
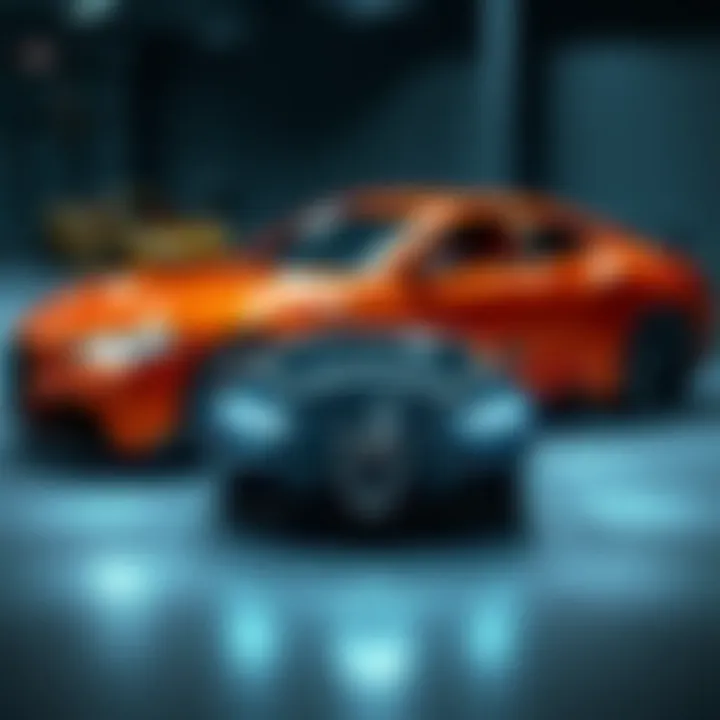
The environmental footprint of rotationally molded polyethylene cannot be overlooked. Although it is generally valued for its durability, the production process itself raises questions about sustainability. The energy consumption required in the molding process is significant, contributing to carbon emissions. Additionally, polyethylene is derived from petroleum, a non-renewable resource. With growing concerns about climate change and resource depletion,
automakers are under pressure to adopt more eco-friendly practices. The growing trend towards biodegradable or recycled materials poses a challenge to conventional polyethylenes. As the industry shifts focus, manufacturers will have to continually innovate in order to balance performance and environmental responsibility.
"Innovation in material selection will not only address waste management but also meet stringent regulations in emissions and material use."
One positive move includes the increased use of recycled polyethylene. Many organizations now offer recycled resin options, which can mitigate the environmental impact. However, the challenge remains in maintaining the properties and performance that are critical in automotive applications.
Production Constraints
The production of rotationally molded polyethylene is also impacted by certain constraints. A common limitation is the relatively longer cycle times when compared to other molding processes, such as injection molding. This can create bottlenecks in production lines, causing delays in product availability. Additionally, high initial tooling costs for molds can be a stumbling block for smaller businesses or startups aiming to enter the market.
Moreover, not all designs are compatible with rotational molding. Complex geometries require precise calculations and adjustments. This can complicate the design process, with engineers needing to navigate the limitations of molding capabilities. It’s a careful balance—strives for innovation must work hand-in-hand with the practical constraints of manufacturing.
Ultimately, while rotationally molded polyethylene stands as a strong contender in the automotive market, it is essential to navigate challenges regarding environmental impact and production constraints. Engaging with these realities will empower industry professionals to embrace sustainable practices without sacrificing performance quality.
Future Insights and Trends
The landscape of automotive materials is shifting, with rotationally molded polyethylene taking center stage. Understanding future insights and trends surrounding this valuable material isn't just academic; it’s crucial for stakeholders looking to innovate and remain competitive. As we plunge into this area, we’ll dissect the major developments and projections shaping its future.
Innovations in Material Science
Recent advancements in material science are setting the stage for enhanced functionalities of rotationally molded polyethylene. Research into copolymers, for example, is leading to formulas that can better withstand environmental stresses while maintaining lightness. These innovations hold promise for applications beyond traditional uses—notably in electric vehicles where battery pack casings and underbody components require materials that resist heat and corrosion.
Integration of nanotechnology is another front-line development. This tech can bolster polyethylene's mechanical properties and impart greater resistance to wear and impact. Imagine vehicles that can brush off the occasional bump without significantly denting or cracking. The results are not merely theoretical; they are being observed in some pilot programs by leading automotive manufacturers globally.
"Incorporating innovations in material science can transform not just products but the perception of what is possible in automotive design."
Market Projections
When considering the future, one can’t disregard market projections. Presently, rotationally molded polyethylene holds a significant share of the automotive parts market. Analysts predict an upward trajectory, with projections estimating growth rates close to 6-8% annually over the next several years. This increase is anticipated due to the shift toward lightweight materials aimed at improving fuel efficiency and decreasing emissions.
Key sectors driving this growth include:
- Electric and hybrid vehicles seeking to balance power and vehicle weight.
- Custom aftermarket parts, where rotationally molded components provide unparalleled design flexibility.
- Sustainability initiatives, emphasizing the use of recyclable materials that resonate with modern eco-conscious consumers.
In summary, as we peer into the future of rotationally molded polyethylene within automotive applications, it emerges as a cornerstone for innovation—fueling both technical advancements and market evolution. This interplay between innovative developments in material science and optimistic market forecasts suggests a robust future ahead, where not only will product functionality rise, but also consumer satisfaction will likely hit new highs.
Case Studies
Case studies serve as a vital part of understanding the practical implications of rotationally molded polyethylene in automotive applications. They offer valuable insights into how this material is utilized in real-world settings, showcasing innovative uses and highlighting both successes and challenges faced during the production and application processes. An in-depth examination of these case studies can illuminate the benefits that rotationally molded polyethylene provides, as well as considerations that automotive engineers need to keep in mind.
Successful Product Implementations
In recent years, numerous automotive companies have successfully integrated rotationally molded polyethylene into various elements of vehicle design. For instance, Ford has utilized this material in the development of their new vehicle storage solutions. One standout example is the cargo management systems used in the Ford Explorer. These systems leverage rotational molding to produce lightweight, durable storage components that enhance the vehicle’s usability without adding significant weight. By using this approach, Ford is able to offer more versatile designs while ensuring that the parts remain cost-effective and reliable.
Another notable case is General Motors, which has incorporated rotationally molded polyethylene in interior applications, specifically within climate control ducts. The durability and lightweight characteristics of this material allow for intricate shapes while maintaining excellent thermal resistivity; essential in ensuring efficient airflow.
Rotationally molded polyethylene’s flexibility doesn't stop at the structural aspects. Companies like Jeep have explored custom branding opportunities by adding unique textures and colors directly into products, allowing for a personalized touch that appeals to consumers. This customization not only meets market demand but also enhances brand identity.
Comparative Analysis
When comparing the effectiveness of rotationally molded polyethylene against other materials commonly used in automotive applications, several key factors come to light. For example, when looking directly at injection-molded plastics, rotationally molded polyethylene often comes out ahead in terms of design flexibility and impact resistance. While injection molding can produce highly detailed components, it typically lacks the capability to create larger parts with uniform thickness, making rotational molding a preferred option for certain applications, especially in automotive designs requiring bulkier components like fenders or bumpers.
Additionally, the production processes for rotationally molded polyethylene generally have a lower environmental impact than other molding methods. This results from the comparatively lower energy requirements and waste generation rates during the manufacturing phase. However, the challenge remains in the recycling of these materials, as the automotive industry pivots towards sustainability. In this aspect, ongoing research strengthens the case for rotationally molded polyethylene as an increasingly eco-friendly option in the market.
Through these case studies, it becomes evident that the versatility of rotationally molded polyethylene opens up numerous possibilities in automotive design. By analyzing successful implementations and conducting comparative assessments, designers can better understand how to leverage this material's properties to enhance vehicle performance and consumer satisfaction.
Ending
Understanding the importance of rotationally molded polyethylene in the automotive sector goes beyond merely recognizing its properties and applications. This material has made significant strides in enhancing the functionality and durability of various automotive components. Its lightweight yet robust nature, combined with inexpensive production methods, positions rotationally molded polyethylene as a favorable choice for manufacturers looking to push the envelope on design while keeping costs manageable.
Summary of Key Points
- Robust Production Process: The production process of rotationally molded polyethylene allows for intricate designs and smooth finishes, making it ideal for both exterior and interior automotive parts.
- Diverse Applications: From dashboards to storage systems, this material finds its place in a vast array of components, showcasing versatility that appeals to designers and engineers alike.
- Cost-Effectiveness: Its affordability, coupled with durability, means that investments in rotationally molded polyethylene often yield significant returns, especially in high-volume production settings.
- Environmental Aspects: Addressing the environmental impact aligns with current industry trends. Manufacturers are increasingly pursuing sustainable practices, and using polyethylene can contribute positively in this regard.
Final Thoughts on Innovation in Automotive Materials
As we venture into an era where innovation is paramount, the role of rotationally molded polyethylene cannot be underscored enough. The material embodies both tradition and forward-thinking in its application, signifying a bridge between proven methods and technological advancements. Advances in material science continue to refine its properties, promising even greater applications in the future. With sustainability becoming a cornerstone for various industries, integrating more eco-friendly practices, like the use of rotationally molded polyethylene, will be key in staying relevant and competitive in the automotive landscape. Embracing innovation in materials not only enhances the product's longevity but also aligns with the expectations of a more environmentally conscious consumer base.
"Innovation distinguishes between a leader and a follower." - Steve Jobs
With opportunities that lie ahead, rotationally molded polyethylene remains a significant player, ready to adapt and evolve in response to new challenges and market demands. As the automotive world continues to turn, so too will the role of materials like this, ensuring we progress towards a more efficient and sustainable future.