Understanding Compressor Costs: Key Insights for Buyers
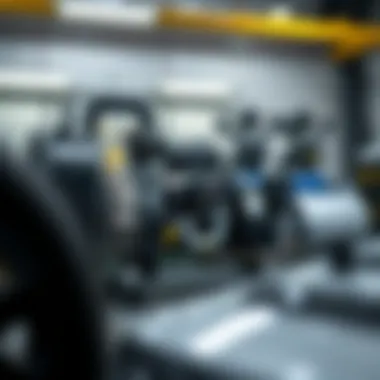
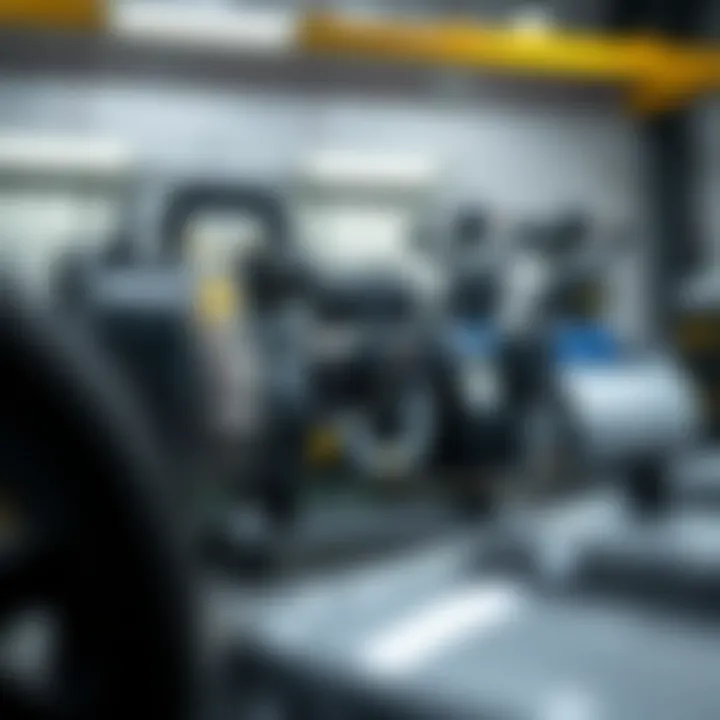
Intro
Navigating the waters of compressor costs can feel like steering a ship through choppy seas. Whether you are an automotive enthusiast looking to upgrade your vehicle's performance or a marine professional contemplating the right compressor for your vessel, understanding the nuances behind compressor pricing is crucial. This article will elucidate the various components that affect costs, from the type of compressor to maintenance needs, and how new technologies impact our wallets.
By breaking down the subject into manageable parts, we aim to provide clarity and actionable insights for both casual buyers and industry professionals. Let’s anchor ourselves in the details and embark on this comprehensive journey through the world of compressor costs.
Prologue to Compressor Costs
In the intricate world of machinery, understanding compressor costs serves as a cornerstone for both industry veterans and newcomers alike. Compressors lie at the heart of numerous applications—spanning from automotive systems to industrial equipment—making their role not just significant, but pivotal. Knowing the costs associated with compressors can save you a pretty penny and ensure wise investments.
One of the striking elements of this topic is the blend of initial expenditure and ongoing operational costs. Not only should one consider the sticker price of the compressor, but also the additional burdens that come with energy consumption, maintenance, and overall longevity. Drill down on these aspects to make sound decisions that echo well beyond the moment of purchase.
Overview of Compressor Functions
Compressors function as the driving force behind many everyday systems, transforming fluid states to fulfill a vast range of functions. At their core, they take in gas, compress it, and discharge it at higher pressure, enabling processes in industries that rely on air conditioning, refrigeration, and countless automotive functions. For instance, in cars, compressors are crucial for air conditioning systems, providing the necessary pressure to circulate refrigerant and cool interior spaces.
Moreover, compressors operate under different methodologies, whether it's a reciprocating compressor suited for high-pressure operations or rotary screw compressors favoring continuous operations with less noise. This diversity necessitates a keen understanding of each type, as the functionalities can greatly affect both installation costs and the overall efficiency in application.
Importance of Understanding Costs
Grasping the cost dynamics of compressors is not merely an academic exercise; it's essential for making practical decisions. The upfront purchase price is just the tip of the iceberg. Subsequently, costs involve electric consumption, parts replacement, and regular maintenance. These factors can accumulate and potentially erode the perceived value of what seemed like a bargain at first glance.
"What you spend at the beginning might not be your final tally."
This reality is particularly pronounced in the automotive and marine sectors, where operational efficiency can impact overall profitability. Hence, a savvy consumer ought to contemplate metrics like total cost of ownership (TCO) to understand how compressors fit into their broader financial picture. Allowing oneself to look past immediate costs opens the door to smarter choices that can yield dividends over time.
In essence, understanding compressor costs extends beyond simple calculations. It encompasses a deeper appreciation of machinery dynamics, operational efficiency, and the wisdom to project long-term financial implications.
Types of Compressors
Understanding the types of compressors is pivotal, especially when delving into the cost dynamics in industries like automotive and marine. Each type offers unique operational benefits, efficiencies, and drawbacks that are essential to consider when making purchasing decisions or upgrades. Here, we lay out the four main types of compressors commonly found in the market: reciprocating, rotary screw, centrifugal, and scroll compressors. This variety caters to different needs, from small-scale applications to larger industrial functions, and recognizing their distinctions can be a game changer in both cost management and performance.
Reciprocating Compressors
Reciprocating compressors are often regarded as the workhorses of industrial operations. They operate by trapping a volume of air or gas and compressing it by a piston moving back and forth within a cylinder. This method provides high efficiency and is particularly useful for applications requiring high pressure and moderate flow rates.
One of the key advantages of reciprocating compressors is their adaptability. They can be configured to handle various gasses, making them versatile in applications from refrigeration to automotive engines. However, they are not without their downsides. The mechanical complexity can lead to higher maintenance costs due to wear and tear. Components like pistons, valves, and connecting rods are subject to significant friction, which can lead to frequent repairs.
Furthermore, they can be noisier than other compressor types, which is an important consideration for urban applications. When weighing cost against operational efficiency, understanding these factors can be crucial for businesses or individuals.
Rotary Screw Compressors
Shifting gears to rotary screw compressors, these machines use two meshing screws to compress air, essentially creating a continuous flow. They shine in heavy-duty, high-demand situations where constant air delivery is essential. Industries dealing with pneumatic tools or large manufacturing operations often favor these for their durability and efficiency.
Benefits of rotary screw compressors include their lower operational noise and higher energy efficiency compared to reciprocating units. Since they run more smoothly, they typically don’t have the same level of wear on components, meaning less frequent maintenance. However, the initial purchase cost tends to be higher, which can be a sticking point for some buyers.
Investing in rotary screw technology might be sound in the long run when you factor in energy savings and reduced maintenance, making it a worthy consideration for businesses looking to streamline operations.
Centrifugal Compressors
Centrifugal compressors stand apart from the others by using a rotating disk to impart kinetic energy to the gas, thereby compressing it. These are predominantly used in gas pipeline applications and industrial processes requiring large volumes of air or gas at relatively low pressures. Their design allows for continuous airflow, which is particularly efficient for large-scale operations.
A significant perk of centrifugal compressors is their ability to handle large capacities with minimal footprint. However, they typically require a higher upfront investment and are usually less efficient at low flow rates compared to reciprocating or screw types. Therefore, they’re best suited for scenarios with consistent demand.
Choosing a centrifugal compressor means focusing on its efficiency and high productivity, especially in settings where downtime must be minimized.
Scroll Compressors
Last but not least are scroll compressors, which utilize two spiral elements—one stationary and one moving—to compress air. They are compact and known for their quiet operation, making them perfect for residential and light commercial uses like HVAC systems.
In addition to being quieter, they offer high efficiency and reliability with fewer moving parts relative to reciprocating compressors. This translates into lower wear and tear, hence lower operational costs over time. The primary concern here revolves around cost, as scroll compressors can be pricier upfront compared to others. However, the savings in energy bills and maintenance can warrant the initial investment.
In summary, when assessing your needs, you’ll want to think about what type of compressor fits your budget and operational requirements best. Be mindful that while the initial costs might vary, looking at the big picture, including longevity, efficiency, and maintenance, can lead to smarter investments in the long run.
Factors Influencing Compressor Costs
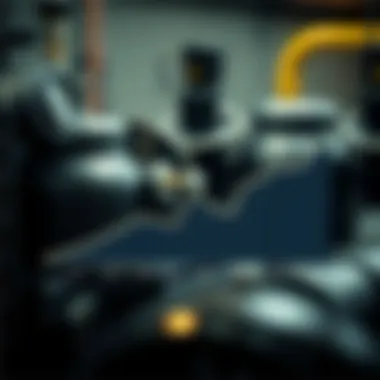
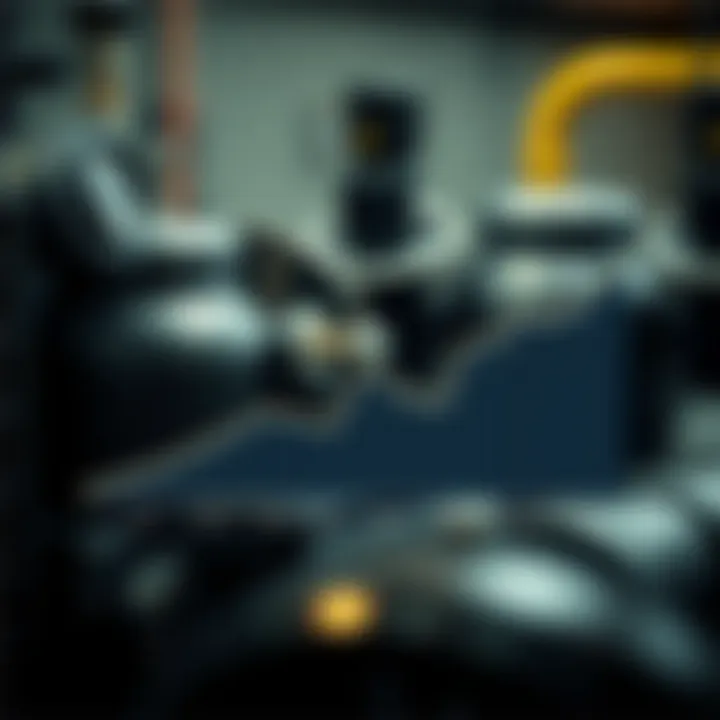
Understanding the intricacies of compressor costs is paramount for anyone involved in the automotive or marine sectors. A compressor isn’t just a component; it’s the heart of various systems, influencing overall efficiency and performance. The costs associated with compressors extend beyond the initial purchase price. Various elements play into what a consumer will eventually pay long-term. When breaking down the factors influencing compressor costs, three key aspects come into focus: material quality, manufacturing processes, and brand reputation. Let's explore how each of these elements impacts pricing and decision-making for enthusiasts and industry professionals alike.
Material Quality
The grade of materials used in a compressor can significantly sway its price. High-quality materials tend to be more durable, which translates to fewer repairs and replacements down the line. For example, using stainless steel components often results in lower corrosion rates, impacting long-term operational costs positively. On the flip side, cheaper materials may lead to frequent breakdowns, which can escalate expenses quickly.
Benefits of High-Quality Materials:
- Increased Lifespan: Components like bearing and housing made from robust materials are less likely to fail prematurely.
- Better Performance: Quality materials can enhance the efficiency of compressors. They can withstand higher pressures and temperatures, which is crucial for both automotive and marine applications.
- Reduced Maintenance Needs: Investing in higher quality could mean fewer issues that would require professional maintenance or part replacements.
Manufacturing Processes
It’s not just what a compressor is made from, but also how it’s made. The manufacturing process involves various steps that can affect not only cost but also the reliability and performance of the compressor. Advanced manufacturing techniques, like precision machining and computer-controlled assembly lines, can produce compressors that operate more efficiently and last longer.
Considerations About Manufacturing Processes:
- Technology Adoption: Companies that incorporate modern automation typically yield fewer defects, affecting overall costs.
- Labor Costs: Manufacturing processes in different countries include differing wage scales, which can ultimately affect the final pricing of the compressor.
- Environmental Standards: Compliance with regulations can factor into costs as well. Plants that adhere to high environmental standards may have higher operational costs, which can be reflected in the pricing.
Brand Reputation
Last but not least, brand reputation plays a pivotal role in the pricing of compressors. Well-established brands often command higher prices because of trust and reliability. Customers are often willing to pay a premium for a brand known for producing durable, efficient compressors. Conversely, newer or less-known brands may under-price their products to penetrate the market.
Factors Influencing Brand Impact:
- Customer Reviews: Positive feedback can enhance a brand's standing, potentially justifying a higher price point.
- Service Availability: Brands with a detailed service network might cost more upfront but save users from unexpected repair costs later.
- Warranty Options: Longer factory warranties generally indicate confidence in a product’s reliability and can influence consumer buying decisions.
Ultimately, understanding these factors can provide valuable insights into what affects compressor costs. It's important for buyers, whether they are automotive enthusiasts or marine operators, to consider these aspects to ensure they are getting the best value for their investment.
Initial Purchase Costs
When diving into the world of compressors, understanding the initial purchase costs becomes paramount. This segment of the analysis will shed light on various elements that play a crucial role in determining these costs, as well as their benefits and considerations for buyers. The initial cost of a compressor isn't just about the price tag you see at the store; it’s a number influenced by various factors that can impact your savings and efficiency in the long run.
Retail Pricing Trends
The retail pricing trends for compressors can be as changeable as the weather in springtime. Prices can fluctuate based on numerous factors, including economic conditions, supply and demand, and technological advancements. For instance, during times of economic boom, manufacturers may increase prices anticipating higher consumer spending. Conversely, during downturns, prices might fall as competition heats up among brands eager to attract customers.
Factors like material costs and the availability of skilled labor can also tilt the scales. A surge in the cost of raw materials like steel or aluminum, which are essential for compressor construction, often leads to a hike in retail prices. Moreover, new technologies are continuously making it onto the market, which can lead to enhanced efficiency, but they can also command a higher price.
- Economic Conditions: Broader economic trends have a significant impact on pricing.
- Material Costs: The price of raw materials can sometime make or break the final cost.
- Technological Advances: New, efficient technologies can skew pricing trends upward.
For potential buyers, keeping an eye on these trends can be key. By understanding the factors driving retail prices, you’ll be better equipped to make informed decisions that suit your budget, ultimately leading to savings when it counts.
Cost Comparison Across Types
The world of compressors is diverse, each type bringing its unique attributes, which has implications on pricing. When comparing costs across various types of compressors, it's vital to consider not just the upfront cost but also how each type can serve your specific needs.
- Reciprocating Compressors are generally known for their lower purchase price, making them an attractive option for budget-conscious buyers. However, these may require more frequent maintenance.
- Rotary Screw Compressors, while typically more expensive upfront, can offer high efficiency and lower long-term operational costs.
- Centrifugal Compressors are excellent for high-capacity needs but come with a hefty initial investment.
- Scroll Compressors fall somewhere in the mid-range both in terms of initial cost and operational efficiency.
The key takeaway is to match the compressor type to your specific application. For individuals or businesses focusing on long-term investment, it’s often wise to look beyond the initial purchase cost and decipher what each model would potentially save or cost you over time. Understanding the nuances among these types can lead to a smarter purchasing decision that translates to long-term benefits.
What you pay at the outset often folds into what you’ll pay throughout the compressor’s lifecycle, making careful consideration crucial.
In essence, initial purchase costs set the stage for your compressor ownership journey. By grasping these points, buyers can elevate their understanding, enabling them to align their investments with their operational needs.
Ongoing Operational Costs
Ongoing operational costs are a significant aspect of owning and maintaining compressors in both automotive and marine applications. Understanding these expenses helps consumers make informed decisions and appropriately budget for long-term ownership. Failing to consider ongoing costs can lead to unexpected financial burdens that may outweigh the initial savings seen during a compressor's purchase.
The continuous expenses associated with compressors can be categorized mainly into energy consumption and maintenance and repairs. Each of these factors plays a vital role in the total cost of ownership and directly influences the overall financial strategy for anyone investing in compressor technology.
Energy Consumption
Energy consumption is one of the most pressing operational costs you’ll face. Compressors require a substantial amount of energy to function effectively, especially in applications that demand high performance. Understandably, this heavy reliance on power can lead to soaring utility bills, making it crucial to assess this factor before choosing a compressor.
To manage energy costs effectively:
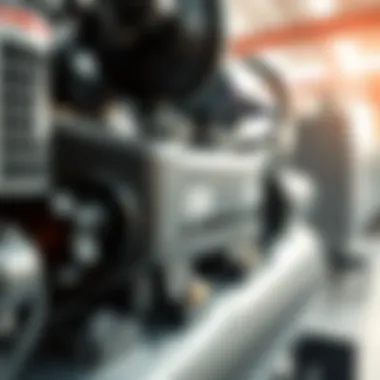
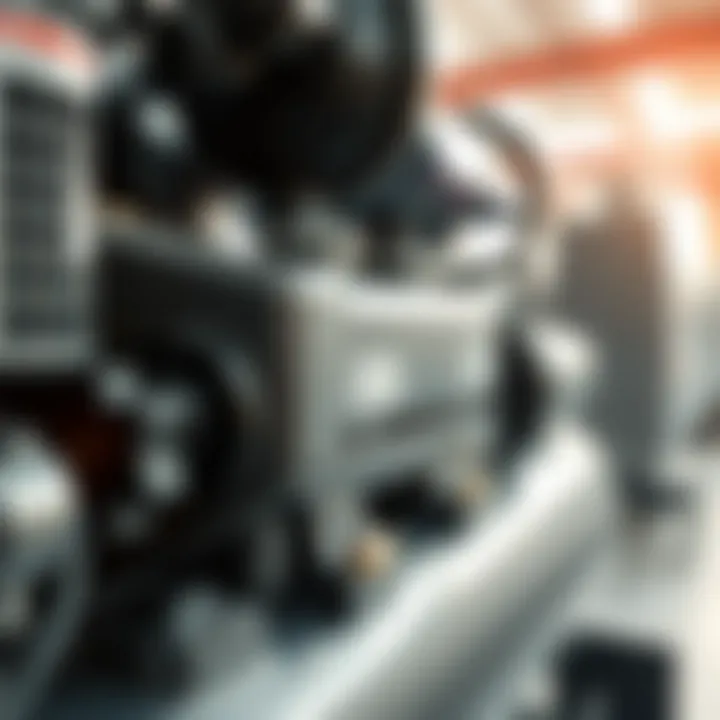
- Select Efficient Models: Consider investing in energy-efficient compressors that are designed to minimize power consumption. Products that comply with standards such as Energy Star or those featuring variable speed drives can help save money in the long run.
- Regular Monitoring: Keeping an eye on energy usage through monitoring software can provide insights into your compressor's efficiency. Identifying unusual spikes in energy consumption can prompt prompt maintenance needs.
In essence, being mindful of energy consumption not only can lower your expenses but also aligns with environmentally conscious practices. Furthermore, better energy management often translates into less strain on the compressor, extending its lifespan and operational reliability.
Maintenance and Repairs
Regular maintenance and potential repairs are another essential component of ongoing operational costs. Although it might seem like a hassle to routinely check up on a compressor, neglecting this aspect can lead to larger problems down the line, often leading to costly repairs or even entire unit replacements.
Maintenance can include tasks such as:
- Inspecting and replacing filters
- Checking and tightening connections and belts
- Ensuring adequate lubrication is maintained
Setting up a routine maintenance schedule can go a long way in preventing unexpected breakdowns. Additionally, keeping spare parts on hand can save time and minimize downtime during repairs, ultimately keeping the compressor running smoothly.
When it comes to repairs, it's important to:
- Understand the warranty: Be aware of what's covered. Some brands offer comprehensive warranties that help mitigate repair costs, but only if you follow their recommended maintenance schedule.
- Consider the cost of technicians: Sometimes the price of hiring professionals can be hefty; opting for training programs to develop in-house maintenance capabilities can be a cost-effective solution over time.
To make the most out of your investment in compressor technology, reviewing all aspects is essential. Visit resources like energy.gov, which offers guidelines on energy efficiency, or reddit.com to engage with communities discussing real-world experiences regarding compressor ownership.
By focusing on both energy consumption and the nuances of maintenance over time, you can balance out the costs and find yourself in a more advantageous position as a compressor owner.
Impact of Technology on Costs
In the realm of compressors, technology is not just a fringe topic; it’s an essential pillar that greatly influences costs. Understanding the link between technological advancements and compressor pricing can empower consumers and industry professionals to make informed choices. As we explore how technology reshapes the landscape of compressor costs, we will look at two specific elements: advancements in efficiency and the integration of smart technologies.
Advancements in Efficiency
The efficiency of a compressor plays a pivotal role in its total cost of ownership. Recent advancements in engineering processes have led to the development of compressors that not only consume less energy but also operate more effectively under various conditions. For instance, modern rotary screw compressors equipped with variable speed drives can adjust their output according to the required demand. This flexibility results in reduced energy consumption, leading to significant savings over time.
With improved materials, like high-performance alloys and composite materials, manufacturers are able to design compressors that can withstand higher pressures and temperatures without suffering wear and tear. This longevity translates into fewer replacements and ultimately lower costs for the end-users.
- Energy Efficiency Ratings: The implementation of energy efficiency ratings, such as the Energy Star label, helps consumers identify compressors designed with modern technology in mind.
- Sustainability Considerations: Many manufacturers are now adopting eco-friendly technologies that reduce emissions, thus appealing to those with environmental concerns in industries like automotive and marine sectors.
These advancements clearly showcase the growing trend to prioritize not only performance but also energy efficiency, revealing a direct correlation between technological improvements and overall cost reductions.
Integration of Smart Technologies
The rise of smart technologies has transformed the compressor market dramatically. Today, compressors can be outfitted with sensors and IoT capabilities that allow for real-time monitoring and data analysis. Such integration can virtually revolutionize maintenance schedules and operational efficiency.
Smart compressors can predict failures before they occur, thus preventing costly breakdowns. For example, if a compressor starts to show signs of inefficiency or overheating, a smart system can send alerts, allowing operators to address issues proactively. This proactive management leads to:
- Reduced Downtime: Minimizing the time an essential piece of equipment is out of service directly cuts costs associated with lost production.
- Better Resource Allocation: By providing insights into operational performance, businesses can allocate resources more effectively, ensuring that maintenance isn’t schedule based on guesswork.
Moreover, cloud-based technologies enable central monitoring and management of compressor systems across different locations, simplifying the management process and allowing for standardized operating procedures.
"With technology shaping the future of compressors, staying updated on trends is crucial for cost efficiency."
Understanding Total Cost of Ownership
Understanding the total cost of ownership (TCO) is essential for anyone considering the investment in compressors, especially in sectors like automotive and marine. TCO goes beyond just the initial price tag; it encompasses a whole range of financial obligations that may arise over the compressor's lifespan. This broader perspective is particularly important fer consumers and industry professionals who must make informed decisions founded on accurate financial projections.
Incorporating TCO in your analysis allows for assessing the long-term implications of a purchase. When looking at a compressor, it's essential to examine future costs, maintenance issues, repair possibilities, energy consumption, and even potential resale values. Not taking these factors into account could lead you to a false sense of security that a low initial purchase price means greater savings overall. Without a sharp eye on the full picture, one might wind up in a sticky situation of unforeseen expenses down the line.
Calculating Long-Term Expenses
Calculating long-term expenses isn't just a number-crunching exercise; it's a strategic approach to understanding how costs add up over several years. Key elements to consider include:
- Energy costs: Compressors generally consume a significant amount of electricity, making it vital to factor in energy efficiency ratings and local electricity rates in your calculations. For instance, an energy-efficient screw compressor may have a higher upfront cost but could lead to savings over time.
- Scheduled maintenance: Regular upkeep can range from oil changes and filter replacements to more complex servicing. Understanding the frequency and cost of these services can give insight into long-term financial demands.
- Potential repairs: Machines can falter with age, and knowing the common issues associated with different types of compressors helps in estimating potential repair costs. A good rule of thumb is to anticipate an increased likelihood of repairs in years five through ten.
Tallying all these expenses over the expected lifecycle of the compressor gives a clearer ticture of the real financial commitment.
Evaluating Resale Value
Resale value can play a pivotal role in determining long-term costs. When a compressor has served its purpose, the potential to recoup part of your initial investment hinges on various factors:
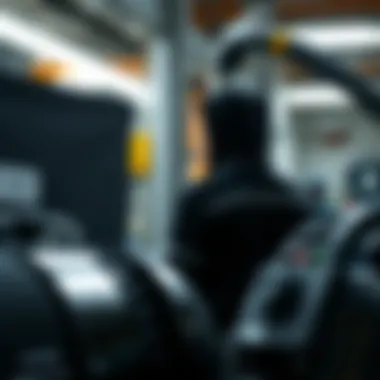
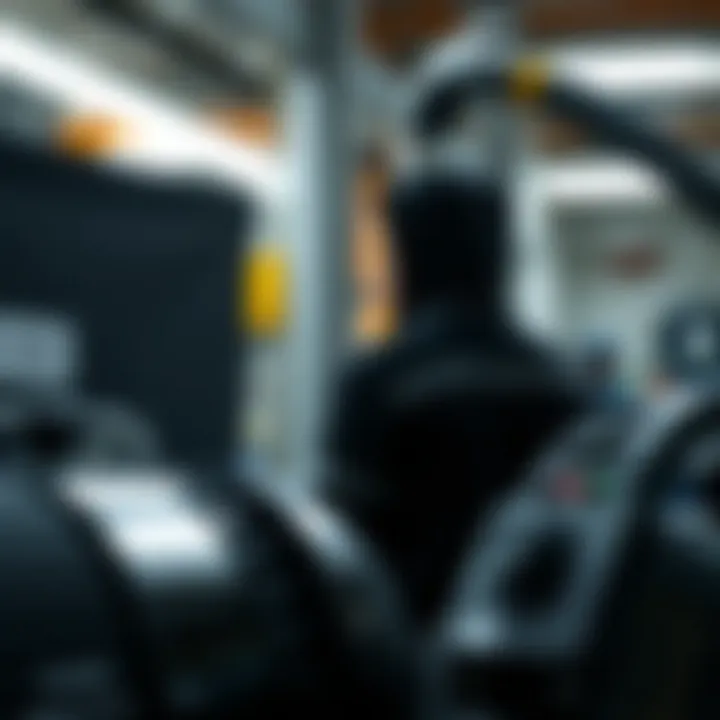
- Condition and maintenance history: A well-maintained compressor can fetch a better price on the resell market, so keeping up with scheduled services can pay off.
- Brand reputation: Brands known for durability and performance often hold their value better than lesser-known ones.
- Technological advancements: As new models with advanced features come into play, older compressors might depreciate faster. However, if your unit has unique attributes or capabilities, it could stand out and retain value.
Understanding the factors affecting resale value equips buyers and sellers alike to make well-informed decisions at the end of a compressor's usable life.
"A stitch in time saves nine" — this adage holds particularly true in maintaining your compressor. Regular attention can save you future headaches and costs.
Comparative Analysis of Compressor Brands
When it comes to compressors, the brand name can often serve as a proxy for quality, reliability, and performance. Therefore, a comparative analysis of compressor brands is a crucial element of this broader discussion on compressor costs. Navigating through the myriad of options available today necessitates a keen understanding of the strengths and weaknesses associated with different manufacturers.
Inspecting various brands can lead consumers to appreciate the influences on pricing and technology. Not all compressors are created equal, and brand reputation can reflect experience, innovation, and customer service, aspects that are essential for ensuring a high-quality product in both the automotive and marine sectors.
Key Factors to Consider:
- Reputation and Longevity: Established brands may have years, even decades, of engineering and user feedback influencing their designs. A brand that's been around longer might be deemed more trustworthy, given their history of performance in the field.
- Warranty Options: Different brands offer various warranty terms. A longer warranty can indicate a manufacturer’s confidence in their product. It provides a safety net for consumers looking to protect their investment.
- Service and Support: How responsive a brand is to customer inquiries and maintenance requests can significantly impact user satisfaction.
High-End vs. Budget Options
The decision to invest in high-end or budget options is often influenced by both immediate and long-term needs. High-end compressors tend to offer advanced features, such as enhanced energy efficiency and superior durability. They often integrate cutting-edge technologies that can adapt to varying operational demands. These compressors might come with a higher initial cost but can save money on energy bills and maintenance down the line.
Budget compressors, on the other hand, present an appealing entry point for those operating under financial constraints. While they may lack some of the advanced technologies and features of their high-end counterparts, they can still deliver solid performance for regular tasks. However, it’s wise to evaluate whether that lower cost comes with trade-offs that could impact long-term value.
"Investing in a more expensive, high-quality compressor can often lead to better efficiency and lower costs in the long run."
User Reviews and Satisfaction
User reviews play a formidable role in assessing compressor brands. Delving into real-world experiences can enlighten potential buyers about the advantages and drawbacks they might not find in product specifications.
- Quality Over Hype: Many high-end brands craft compelling narratives about their products. However, user reviews can cut through marketing fluff to reveal whether those claims hold water in practice.
- Data-Driven Decisions: Ratings and feedback expressed on platforms like Reddit or specialized forums can serve as valuable resources. Consumers often share their stories about performance, repairs, and customer service, which helps in shaping better purchasing choices.
- Overall Satisfaction: Checking how satisfied users are with their purchase leads to more informed choices. A brand with consistent positive feedback likely indicates reliability and safety in performance.
Future Trends in Compressor Costs
The landscape of compressor costs is shifting beneath our feet, influenced by an array of factors that echo changing technologies, market dynamics, and consumer preferences. Understanding these future trends is essential for anyone looking to invest in compressors for automotive and marine applications. Keeping an eye on these developments can help consumers, businesses, and market players make informed decisions, ultimately affecting their bottom line.
Market Forecasts
Predictions for the compressor market indicate a steady growth trajectory over the next several years. As environmental regulations tighten and demand for energy-efficient solutions rises, manufacturers are pivoting to create compressors that not only meet these mandates but also improve overall performance.
- Growing Demand for Efficiency: The push towards eco-friendly solutions is causing a surge in demand for compressors that minimize energy consumption. Companies such as Atlas Copco and Ingersoll Rand are investing heavily in innovative designs that prioritize energy efficiency.
- Expansion in Emerging Markets: Countries in Asia and Latin America are witnessing an uptick in industrial activities, driving the need for compressors in construction, manufacturing, and other sectors. As the infrastructure develops in these regions, so does the market potential for compressors.
- Technological Integration: The forecast also shines a spotlight on the integration of IoT and smart technologies into compression systems. This capability allows for real-time monitoring and predictive maintenance, ultimately resulting in cost savings and operational efficiency for users.
Companies are predicting an average annual growth rate of around 4.5%, which suggests an optimistic future as industries adapt and expand. Understanding these forecasts assists consumers in anticipating changes in market prices and availability, guiding their investment decisions accordingly.
Innovations Shaping Pricing Models
The compressor industry is not just evolving in terms of technology; it's also witnessing a revolution in pricing models. As competitive pressures mount, companies are exploring new ways to structure their prices. Here are some innovations that are changing the game:
- Subscription-Based Models: Some manufacturers are offering compressors on a subscription basis, similar to software as a service (SaaS). This approach allows companies to access the latest technology without the burden of a hefty upfront investment. It encourages more businesses to adopt advanced systems since they can allocate costs over time.
- Dynamic Pricing: Inspired by various industries adopting flexible pricing strategies, compressor companies are looking into dynamic pricing while considering factors like demand changes and product availability. For consumers, this means potential savings during promotional periods or slower seasons.
- Pay-Per-Use Models: Another noteworthy innovation is the pay-per-use model, allowing companies to only pay for the compressor time they utilize. This approach aligns better with project-based industries where equipment needs can be sporadic, providing financial flexibility.
In summation, the future trends in compressor costs point toward a marketplace that is increasingly influenced by technological advances and a growing emphasis on efficiency. Keeping tabs on these predictions and innovations can equip consumers and businesses alike to make smart choices in a landscape that can easily become confusing. Understanding these shifts is not just beneficial; it’s essential.
"Embracing innovation now can lead to significant savings and enhanced performance down the road."
For further insights into market trends, check out Statista.
Finale
The conclusion wraps up the extensive examination of compressor costs presented in this article. It serves as a vital element to distill the key insights gained from our deep dive into the various components that influence pricing and ownership of compressors in the automotive and marine sectors. Without a clear understanding of these topics, consumers and industry professionals might find themselves at a disadvantage when making purchasing decisions.
Summarizing Key Points
By reviewing the significant sections of the article, several points emerge:
- Types of Compressors: We explored the pros and cons of various compressor types, including reciprocating, rotary screw, centrifugal, and scroll compressors. Understanding their functionalities helps buyers pick the right tool for their specific needs.
- Factors Influencing Costs: The costs can fluctuate wildly based on material quality, manufacturing techniques, and the brand’s reputation. Not all compressors are created equal, and knowing where these variances come from can inform a better buying decision.
- Operational Costs: Beyond the initial purchase, ongoing expenses such as energy consumption and maintenance can add up quickly. A comprehensive analysis uncovers the long-term responsibilities linked to compressor ownership.
- Technological Impacts: Innovation has a monumental role in shaping compressor prices. From improved efficiency to smart technologies, understanding these advancements allows consumers to appreciate potential cost savings over time.
- Total Cost of Ownership: Whether determining long-term expenses or appraising resale value, considering the total cost of ownership gives a clearer picture of the financial commitment involved with managing compressors.
- Future Trends: Insights into market forecasts and emerging technologies paint the future landscape of compressor costs, preparing businesses and individuals for what lies ahead.
"Knowledge is power, especially when confronted with significant purchases or investments."
Final Thoughts on Cost Considerations
Reflecting on cost considerations goes beyond mere numbers. It's essential for buyers to think holistically about compressor ownership. Decisions should be based on a balance of initial purchase prices against long-term savings and overall efficiency. For example, a cheaper compressor might seem like a good deal up front, yet its higher operational costs can erode any savings made initially.
Additionally, contemplating the environmental impact is vital. With rising awareness of sustainable practices, eco-friendly compressors might come with a higher price tag but offer long-term savings and less harm to the environment in operational use.
In closing, making a well-informed decision about compressors involves a thorough understanding of their costs—both upfront and ongoing. Each facet discussed in this article builds towards a comprehensive view, allowing automotive and marine enthusiasts to navigate the marketplace with confidence.